MITICA’s cryopump pumping section passes qualification
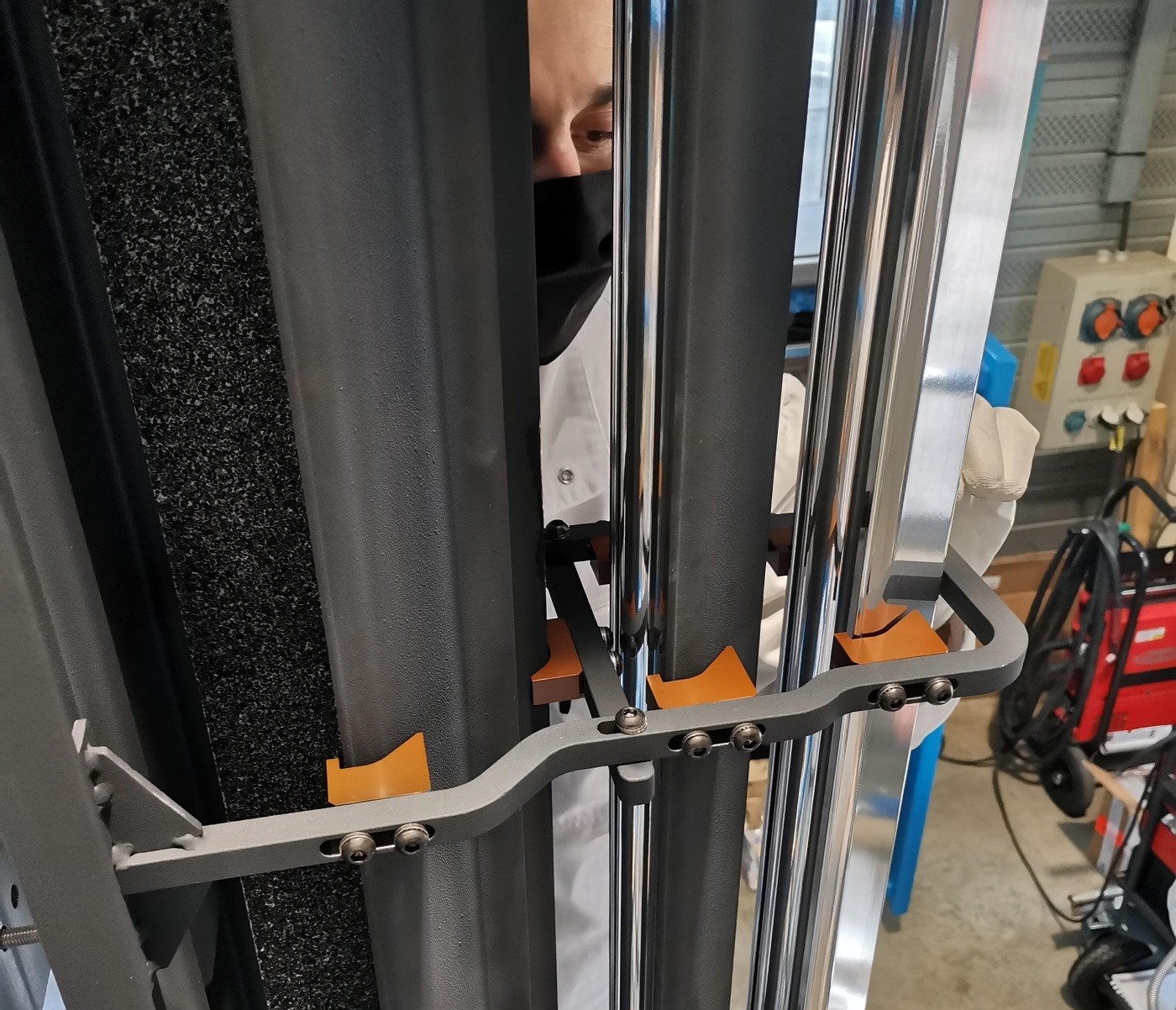
A SDMS technician performing a visual inspection of the brace assembly. A charcoal coated cryopanel can be seen on the left, as well as three blackened thermal radiation shields. SDMS, Saint-Romans, France, April 2021.
MITICA is the prototype of the neutral beam system for ITER. This part of the machine will provide a powerful beam of particles to heat the plasma contained in the vacuum vessel. The neutral beam will also operate in vacuum, hence the need for a cryopump that ensures these conditions.
The MITICA cryopump will provide vacuum by using 64 pumping sections. F4E and its contractor, SDMS, have already manufactured, assembled and tested a mock-up pumping section successfully, which allows the qualification of this component and the start of the serial production of the real ones.
Dimensional inspection is one of the tests that the pumping section has successfully passed. It is a comparison between the physical object and a digital model of it. The F4E Metrology Team probes some points on the physical object with a laser tracker. The 3D coordinates of the probed points are then transformed into the coordinate system of the 3D digital model to assess the compliance with the design tolerances. “What seemed a rather standard metrology task on paper, turned out to be less so once we set foot in the workshop. Stability of the inspected part and of the surrounding environment are necessary conditions to obtain reliable results, but they are not always granted in a manufacturing workshop,” explains F4E metrologist Giacomo Calchi.
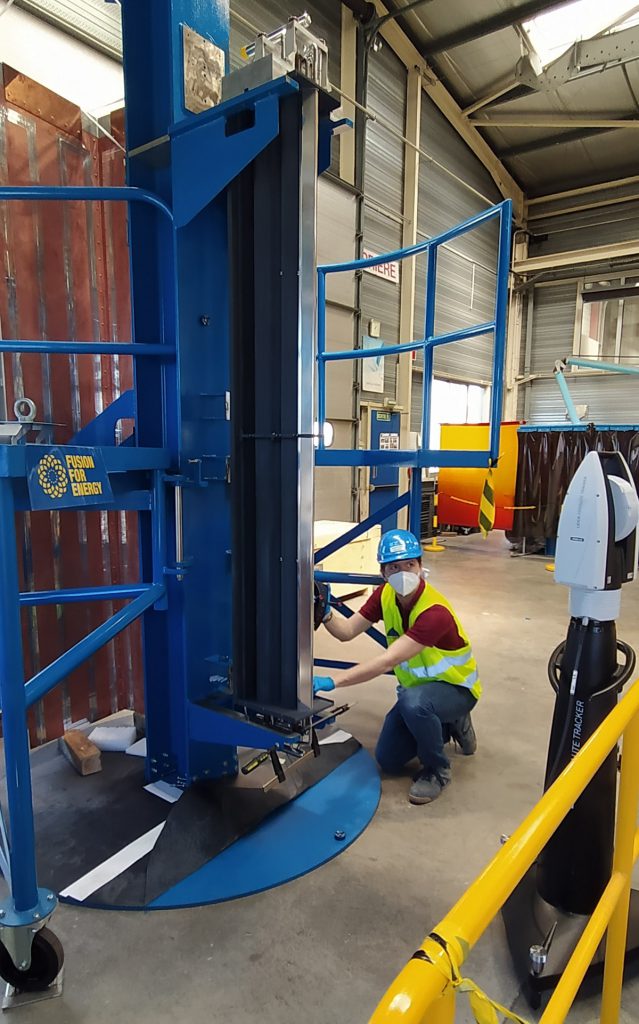
As if that were not enough, the pumping section is composed of different elements with a variety of materials (such as special plastics, aluminium and stainless steel among others), surface treatments and special processes. For instance, cryopanels are charcoal coated, as this material has high effective surface to trap particles when cooled down to around 4K, thus producing vacuum in a process called cryosorption. Thermal radiation shields, by contrast, are blackened on the surfaces that are in front of the cryopanels to intercept as much thermal radiation as possible and emit it to low energy once they are cooled down to 80K. However, they are chemically polished on the rest of the surfaces in order to reflect as much thermal radiation as possible to avoid the heat up of the cryopanels.
“The fact that we could not attach reference points to the part’s surfaces just added to the complexity of the task. With the help of our hosts at SDMS and a bit of ingenuity we managed to overcome these difficulties,” continues Giacomo Calchi. Around 500 points were inspected from four different laser tracker positions around the component; the measurement uncertainty of the 3D coordinates of the points turned out to be less than 0.1 mm overall.
Although some problems have been encountered, the rest of the tests including leak testing, pressure testing, cleaning testing and thermal cycle testing have been passed. “The successful results of these tests have been achieved thanks to the fruitful collaboration of ITER Organization, RFX, SDMS and F4E, which was started by Aurélien Rousseau (former Project Manager for this project) and allows us to proceed with confidence to the serial production” states F4E Technical Project Officer Daniel Dupuy.
“The qualification of the pumping section assembly and subsequent release of their serial production together with the preparation of the manufacturing of the cryopump frame and other components sets us on the road to the assembly of the MITICA cryopump,” concludes F4E Project Manager Grigory Kouzmenko.