Europe’s Inner Vertical Target prototype passes all factory acceptance tests
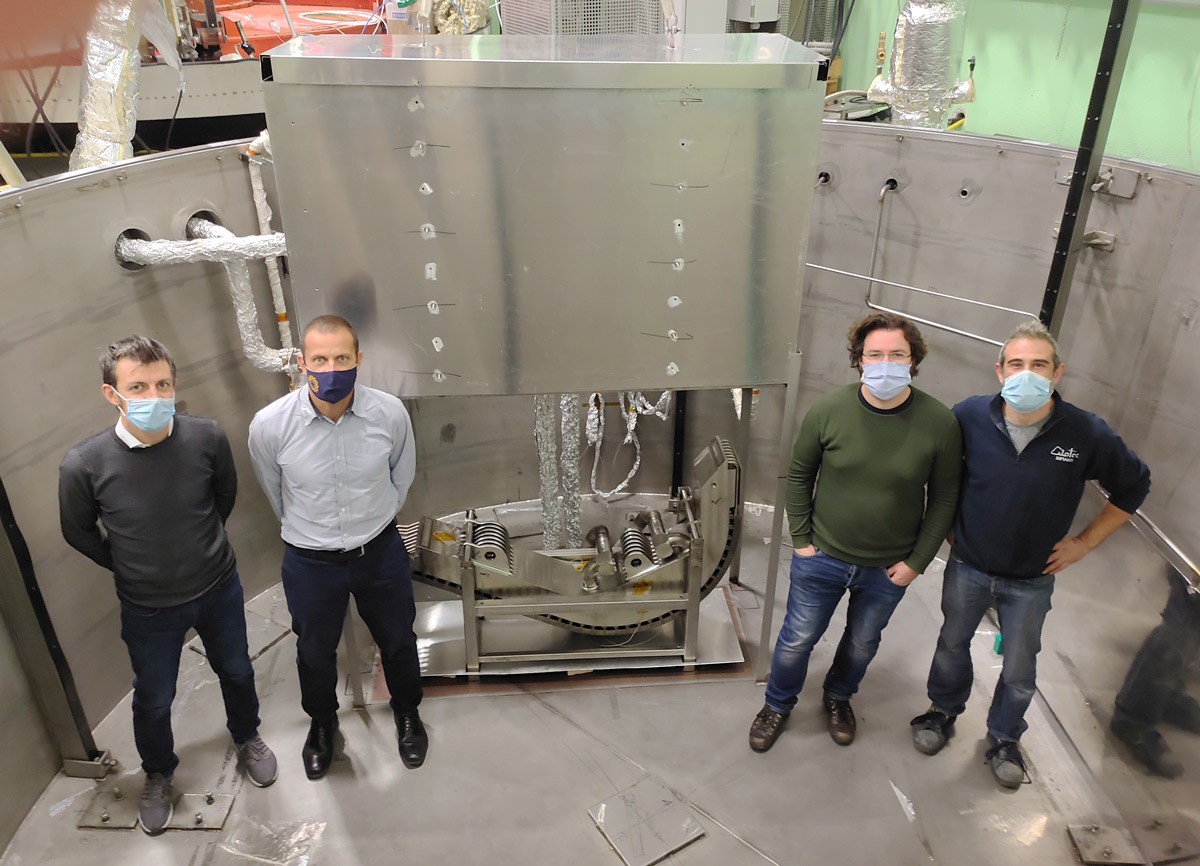
(L-R) Marco Roveta, Criotec Impianti, Pierre Gavila, Fusion for Energy, Massimiliano Palermo, Ansaldo Nucleare, Stefano Galignagno, Criotec Impinati, standing next to the first-ever ITER Inner Vertical Target prototype having successfully passed final acceptance tests.
The ITER Divertor, located at the lower part of the vacuum vessel, will be amongst the components that will experience some of the highest temperatures reached in the biggest fusion device. It will be equipped with an armor of several thousand tungsten blocks cooled down by pressurised water flowing through a circuit of copper alloy pipes. Like a soldier in the line of fire, the Inner Vertical Target (IVT) will be there to intercept the flux from the super-hot plasma particles.
The production of the first-ever IVT prototype had pushed Europe’s engineers into uncharted waters. Was it going to be possible to transfer its design from the drawing board to the factory? Today we know the answer is yes! Almost two years ago, a wooden box containing the first-ever IVT prototype travelled from the factory of Ansaldo Nucleare to Russia’s Efremov Institute to go through a series of heat flux tests. Five months, the box was sent back to Italy from Russia with love, certifying that the prototype had successfully passed them. Now it was up to F4E and Ansaldo Nucleare to ensure that the last stages would be concluded without any glitches.
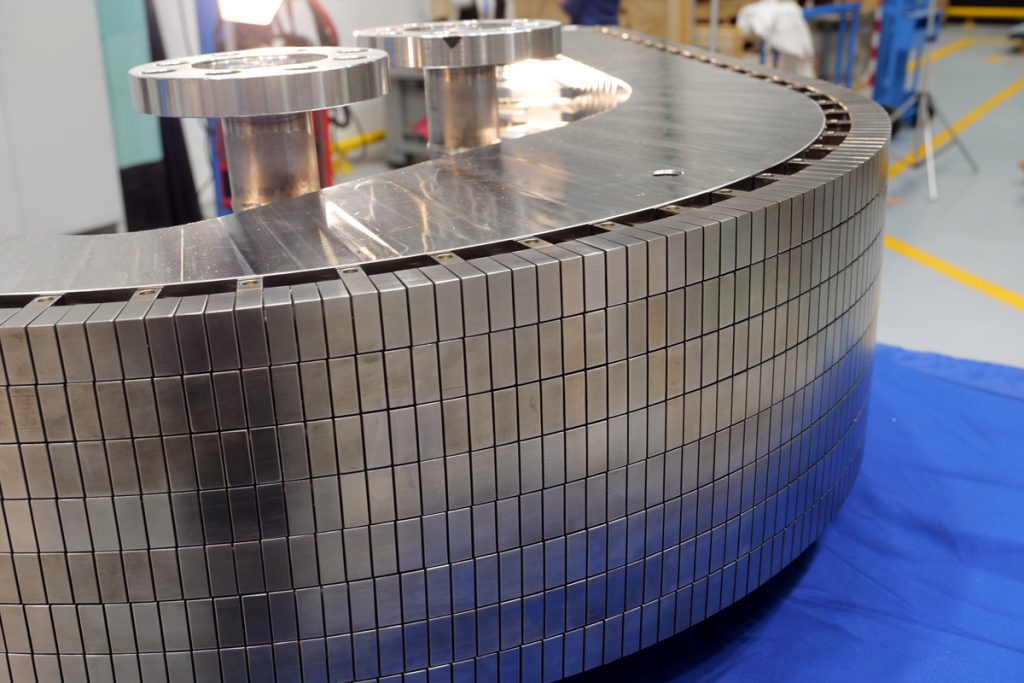
For almost a year engineers worked relentlessly on this prototype to complete its manufacturing cycle. First, they used laser and TIG welding techniques to firmly attach it on its structure. Then, a series of non-destructive, pressure and hot helium leak tests at 250 °C were performed to ensure that the component is qualified for the ITER environment. It passed every threshold concluding successfully the factory final acceptance tests.
“We are pleased to see that the first IVT prototype has consistently performed well,” explains Pierre Gavila, F4E In-Vessel, following this contract. “Early next year we will be sending it to ITER Organization to go through a series assembly tests. This result is very encouraging in view of the many challenges to come linked to IVT procurement.” The F4E strategy foresees the development of three other IVT prototypes with other companies in order to assess the readiness of Europe’s industry to produce this component. The procurement for the IVT series is expected to be launched in 2022.
Marco Grattarola, Ansaldo Nucleare Divertor Team Project Manager, comments on the importance of this milestone. “We, at Ansaldo, are proud of the fabrication of the Inner Vertical Target prototype which complies with all stringent ITER requirements. We met the challenging assembly tolerances, successfully performed heat flux tests up to 20 MW/m2 (simulating ITER conditions), and recently completed the hot helium leak tests. The results reaffirm the soundness of the Ansaldo fabrication strategy. The IVT prototype produced by Ansaldo Nucleare, in partnership with ENEA, and with the important involvement of the Ansaldo Energia workshop, and Walter Tosto as subcontractor for the supply of the steel support structure, demonstrates that this is a real pre-production component.”