F4E and VTT advance remote handling solutions for ITER
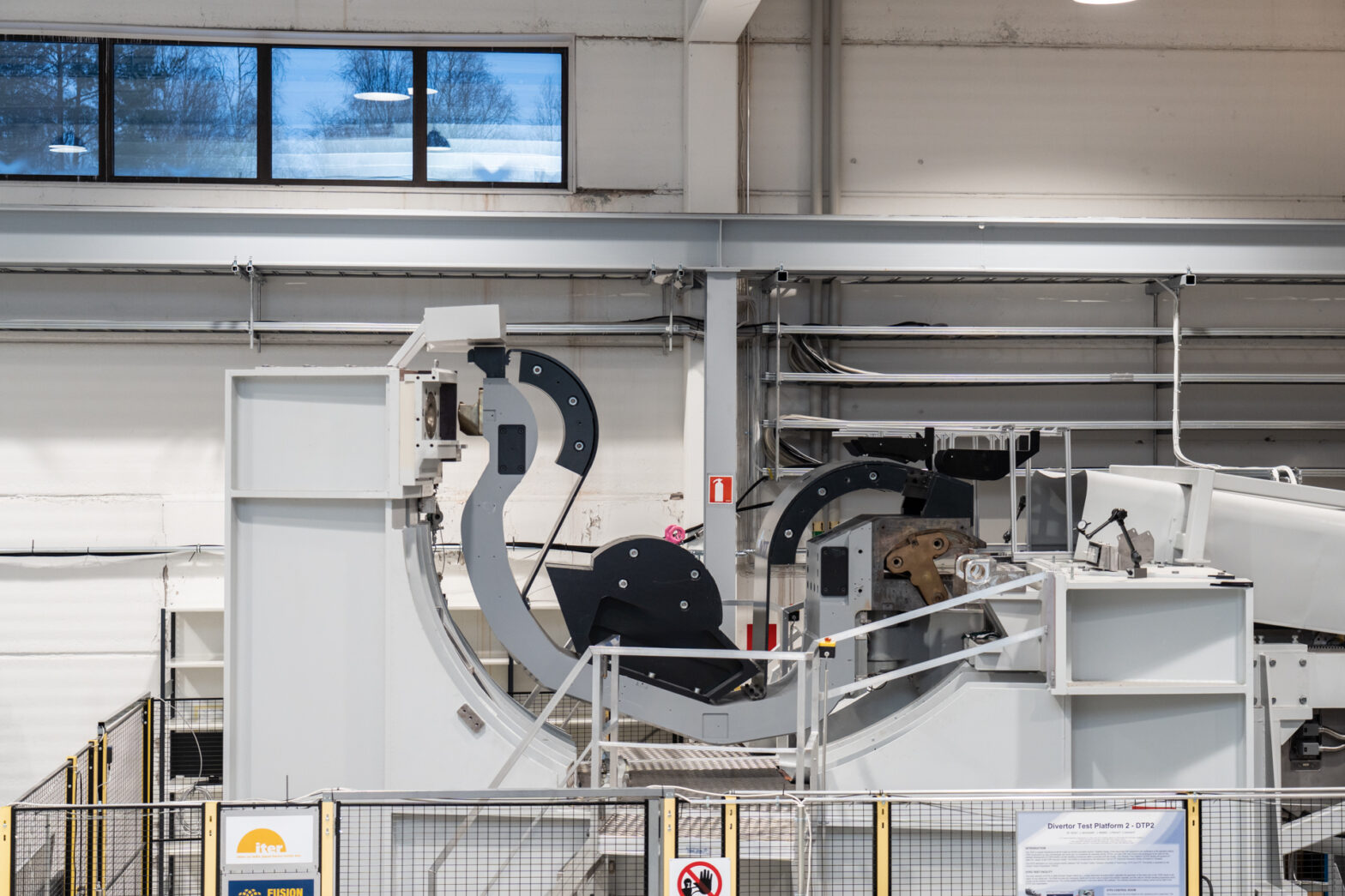
View of the ITER Divertor Cassette prototype at DTP2, Finland, after the successful tests in January 2024. ©VTT
Assembling and maintaining ITER, the massive fusion reactor made up of around one million components, will rely on advanced robotics to access areas where humans cannot. Remote handling systems will work in the heart of the device to manipulate some of its parts in a safe and precise manner.
One of these operations will take place at the lower part of the vacuum vessel. There, a set of special tools will be dedicated to transporting, positioning and extracting the 54 cassettes that make up the divertor. This component forms a doughnut-shaped ‘ashtray’ that will collect exhaust gases and impurities and will face extreme heat loads. For this reason, the cassettes will need to be replaced periodically. This means carrying the 10-tonne components through the tight spaces of the port while staying within millimetric routes.
Europe, responsible for ITER’s divertor remote handling system, is investing in cutting-edge robotics to perform such delicate manoeuvre. Since 2008, Fusion for Energy (F4E) has been collaborating with VTT to develop its key technologies. The Finnish research centre, based in Tampere, built the Divertor Test Platform (DTP2) for this purpose, including a full-scale mock-up of a cassette. Last year, the F4E team travelled there to witness a flawless drill of some of the systems.
This partnership will continue thanks to a new grant signed by both entities this week. The three-year agreement includes an updated scope of tasks, linked to the revised baseline of ITER. The new plan foresees the earlier integration of the divertor into the machine.
To meet this new timeline, F4E is working on the design of the Divertor Assembly Transporter (DAT). “This is a non-nuclear version of the nuclear-grade tool we were developing. The DAT will combine manual operation with remote control, using the solutions validated with VTT,” explains Salvador Esque, remote handling engineer at F4E. Through the grant, F4E will refine and test some of the technologies that will be part of the system. This will help speed up the next phase: the final design and manufacturing of the DAT, which F4E will entrust to a supplier from next year.
“VTT brings us an unmatched know-how in robotics, skilled operators, a bespoke test environment, as well as local subcontractors to support in aspects like hydraulics,” claims Esque. In fact, among other tasks, VTT will team up with Tampere-based companies Coresbond and Fluiconnecto to upgrade the DigiValves. This water hydraulic digital valve system was custom-made by VTT and its partners to improve the reliability of the robot’s movements inside ITER.
Besides the mechanical parts, VTT and its partners also engineered advanced control systems. Operators in ITER will be able to operate the robots in real time thanks to smart tools like the GENROBOT software by GTD or virtual reality applications. In the next years, the teams will work to enhance and test some of the tools, which F4E plans to apply in other European remote handling systems.
But thinking outside the box, some of these innovations show real promise beyond fusion. This is the case of 3D Node, a high-accuracy machine viewing system developed for DTP2. The spin-off company Operview is now demonstrating its potential to teleoperate industrial vehicles, starting a market transition with the support of F4E’s Technology Transfer Programme.
“These innovations are a great example of how the intersection of large engineering projects like ITER with applied sciences can lead to breakthroughs with wider commercial possibilities. We’re proud to continue our collaboration with F4E and build on the expertise we’ve developed together,” said Laura Gonçalves Ribeiro, Project Manager for VTT.